Introduction
In 2020 the International Federation of Knitting Technologists (IFKT) was looking forward to celebrating its 50th Congress however due to Covid19 this was paused and now in 2022 the 50th biennial Congress event of the IFKT will take place in Belfast hosted by Ulster University.
This leading conference in knitting technology and analogous technologies provides an opportunity for both researchers, practitioners, and industry to exchange new ideas and practical experiences from a diverse range of knitting expertise.
The role of knitting technology both warp and weft cuts across many fields including fashion, interiors, sport, military, medical, automotive, aerospace, fibre technology, Computer Aided design, smart textiles, and technical textiles.
The theme of sustainability is an essential approach in all that we do, sustaining future practice, being sustainable in design and sustaining our knitting industry.
IFKT 2022 while celebrating its 50th milestone seeks to encourage dialogue and discussion among participants about general topics as well as this year’s special theme.
We invite various types of contributions from researchers, educators, practitioners, and industrialists to address the broad spectrum of knitting technology challenge.
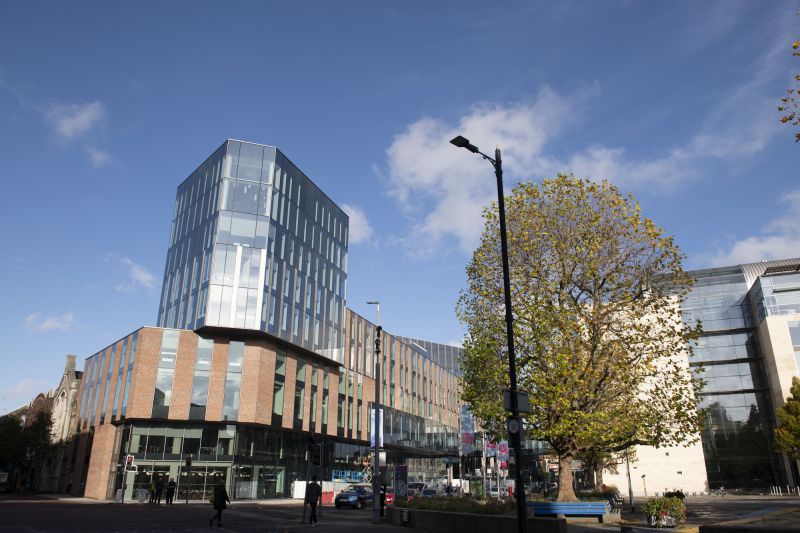
Important Dates
- 30th June – Abstract submission extended to the 14th July
- 21st July – Author notifications
- 23rd July Early bird registration deadline
- 21st August – Camera Ready Full Version of the Manuscript
- 30th August – Final Version of all accepted contributions for publication post congress
Submit your full paper template by 21st August.
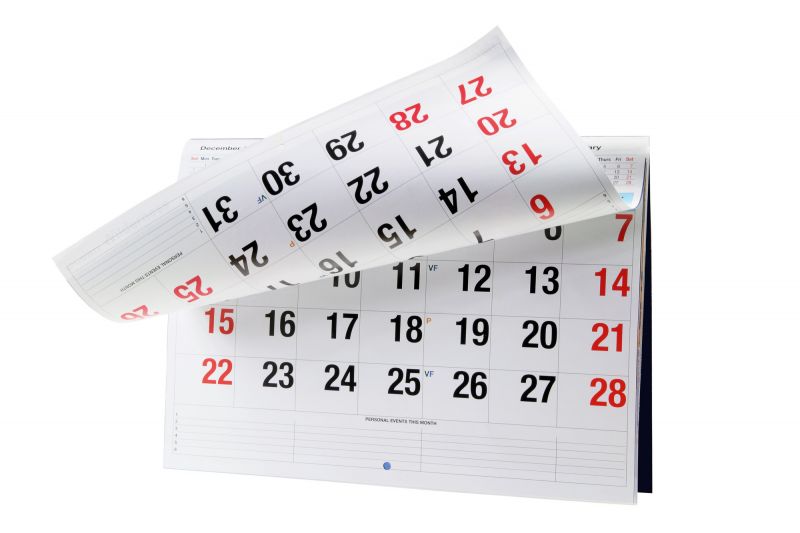
Registration
- Early Registration (3rd July)- £300
- Regular Registration (4th July – 31st August) - £350
- Student Registration - £200
- Non-participant Registration - £200
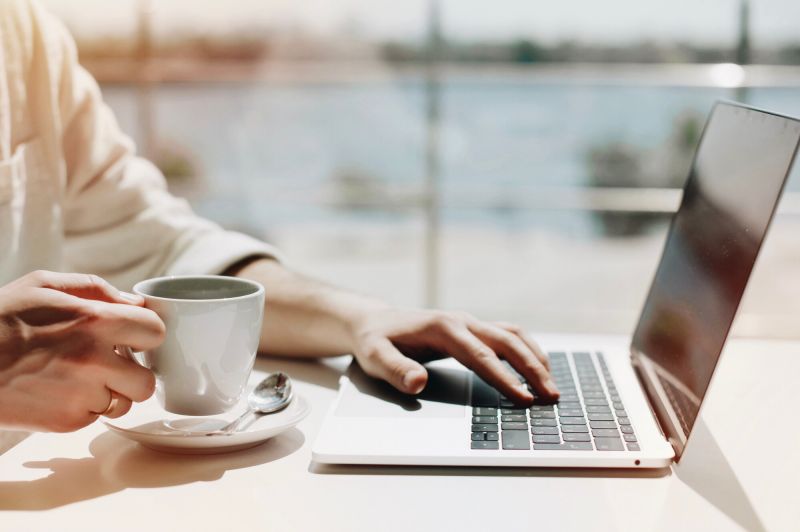
Join us at the IFKT2020 Gala Evening Event
Thursday 1st September, 7:30pm to 10:30pm
Titanic Hotel, Belfast
Programme
Central Board Meeting of IFKT – Room TBC Ulster University, York Street Belfast
Time | Activity |
---|---|
6pm to 7pm | Registration |
6:30pm to 7:30pm | Welcome meeting at Ulster University, York Street |
Time | Activity |
---|---|
8:30am to 9:00am | Registration, Tea and Coffee – BA-01-009 |
9am to 9:10am | Introduction and welcome |
9:10am to 9:30am | Opening Ceremony |
9:30am to 9:50am | Keynote 1 Shima Seiki - Simon Peach |
9:50am to 11:10am | Session 1 9:50am to 10:10am 10:10am to 10:30am 10:30am to 10:50am 10:50am to 11:10am |
11:10am to 11:40am | Tea/Coffee break |
11:40am to 1:00pm | Session 2 11:40am to 12pm 12pm to 12:20pm 12:20pm to 12:40pm 12:40pm to 1pm |
1:00pm to 2:00pm | Lunch |
2:00pm to 4:00pm | Session 3 2pm to 2:20pm 2:20pm to 2:40pm 3pm to 3:20pm |
3:20pm to 3:50pm | Tea/Coffee break |
3:50pm to 5:30pm | IFKT General Assembly |
7:30pm | Gala Evening at Titanic Hotel, Belfast |
Time | Activity |
---|---|
9:00am to 9:30am | Registration, Tea and Coffee at BA-01-009 |
9:30am to 9:50am | Keynote 2 Textiles as a foundational industry - InvestNI - Richard Pelan |
9:50am to 11:10am | Session 4 9:50am to 10:10am 10:10am to 10:30am Irish Spinning: Developing A local Natural Fibre Supply chain - Comingling hemp, wool and polymer fibres for sustainable solutions - Steve Howard and Alison Gault 10:30am to 10:50am 10:50am to 11:10am |
11:10am to 11:40am | Break - Tea and coffee |
11:40am to 1:10pm | Session 5 11:40am to 12pm 12pm to 12:20pm 12:20pm to 12:40pm 12:40pm to 1pm |
1pm to 2pm | Lunch |
2pm to end | Closing remarks - to the next IFKT |
Saturday 3rd September
Optional Trip: TBC
Organising Committee
- Alison Gault
- Katie Mulholland
- Louise Harbinson
- Hazel Bruce
- Fintan Mulholland
- Mary Callan
Scientific Committee
- Yordanka Angelova – Technical University, Bulgaria
- Mirela Blaga - Gheorghe Asachi Technical University of Iaşi, Romania
- Ellen Bendt - University of Applied Science, Niederrhein, Germany
- Alison Gault – Ulster University, Northern Ireland
- Yordan Kyosev – Technical University of Dresden, Germany
- Arzu Marmarali – Ege University, Turkey
- Berndt Meyer, IFWS Landessektion Schwiez, Switzerland
- Elżbieta Mielicka - Textile Research Institute, Poland
- Zbigniew Mikołajczyk, Łódź University of Technology, Łódź, Poland
- Shin Woong Park , Inha University, Incheon, South Korea
- Katarzyna Pieklak – Łódź University of Technology, Łódź, Poland
- Islam Shamimul, IFKT Section Bangladesh, Bangladesh
- Eyal Sheffer, Shenkar College of Engineering and Design, Israel
- Zlatko Vrljicak - University of Zagreb, Faculty of Textile Technology, Croatia
- Hitesh Kumar Sharma - CQA-Seneca College, Toronto President IFKT North America
Day 1 - Abstracts
-
Challenges And Possibilities for Alternative Weft Insertion Methods in Warp Knitting – New Possibilities for New Products
Mutschler, Thomas
Hochschule Niederrhein Research Institute Textile and Clothing Technology
For the production of technical textiles with demanding industrial applications, mineral fibre yarns, and carbon fibre yarns are used, among others. Various metal wires are also the starting material for such products and are in widespread use, "Textile technology knits what cannot be bent and shaped".
With an unlimited structural design, flat knitting offers technological advantages in the production of hoses made of technical materials and complex components, such as profiled hoses. For the production of technical textiles with demanding industrial use, mineral fibre yarns and carbon fibre yarns are, among others, used. Various metal wires are also the starting material for such products and are in widespread use, "Textile technology knits what cannot be bent and shaped".
The processing of mineral fibre yarns into multi-chamber hoses or knitted profile hoses, with a continuously inserted core, presents a special technical challenge. The innovative focus of the new flat knitting machine is the device for the continuous feeding of endless core components.
The production of multi-chamber hoses, with a continuously inserted core, is currently carried out in several operations:
1. Production of the knitted tubes
2. Insertion of the core component
3. Sewing over the entire length to fix the core component and produce the profile adapted to the application.
This method is not only time-consuming but also cost-intensive. So far, there is no possibility to automate this process in one step and make the production of profile hoses feasible on flat knitting machines. By using the feeding device in combination with the needle selection technique, complex profile hoses with one or more different cores can be produced in one operation. This makes the production of such complex profile hoses more cost-effective and efficient. In addition, the development of innovative new products is possible.
-
A Computational Tool For Design, Simulation, And Fabrication of Multiple Structured Knits
Eyal Sheffer, Yoav Sterman, Tom Shaked, Shoval Nir and
Ayelet KarmonCIRTex, Shenkar – Engineering. Design. Art
IsraelHighly specified digital control tools for the customization of knitted fabrics is an existing technology, widely used industrially by trained knitters.
Some fabrication challenges inhibit the extent of use of digital customization for knitted products on a mass scale, specifically when complex multiple structured knits are involved. This is due, in part, to physical changes that occur in the overall fabric dimensions, when stitch combinations with different physical attributes are combined within the same fabric. Existing computational tools fail to assist in the simulation and prediction of these overall deformations and the industry as a whole relies on the expertise of highly trained individuals.
The outline shape of the fabric is of specific importance as it is commonly preconfigured to a specific shape and dimension that must be reproducible. In this work, we propose a computational parametric tool for digitally designing and industrially producing knitted fabrics, creating a direct link between design and manufacturability.
The tool includes an integrated physical simulation component for estimating the fabric deformation. It allows users to control different methods of dimensional compensations for each structure within the design and visualize the outcome of the fabric structure. This allows for a better match between the initial graphic intent of the design and the actual physical knitted fabric outcome. Our approach aims to reduce the number of iteration cycles for knitting material samples, especially when knitting highly varied designs and to pave the path for a more streamlined design to manufacture process.
-
Thermodynamic Qualification of Knitted Spacer Fabrics For Use As Insulation Box Insert In The Context Of Refrigerated Transport Containers In The Logistics Sector
Thermodynamic Qualification of Knitted Spacer Fabrics For Use As Insulation Box Insert In The Context Of Refrigerated Transport Containers In The Logistics Sector
Julia Klausmann1, Thomas Mutschler1, Prisca Holderied1, Dominik Güther2, Thomas Freitag2, Matthias Hummel3, Martin Zeitler3, Oliver van Neerven4, Marcus Oliver Weber1, Christof Breckenfelder1,*
1Hochschule Niederrhein – University of Applied Sciences, Research Institute for Textile and Clothing (FTB), Moenchengladbach (Germany)
2Steinbeis Innovationszentrum Energie- und Umwelttechnik (SIZ), Stuttgart / Steinbeis-Transferzentrum Energie- und Umwelttechnik (STZ), Oelsnitz (Germany)
3Hero-Textil AG, Crailsheim (Germany)
4Walther Faltsysteme GmbH, Kevelear (Germany)
Temperature-sensitive products such as refrigerated and frozen goods pose particular challenges for logistics. Against the background of the mobility shift towards electric vehicles and the current challenges of temperature-stable transport in the field of pharmaceutical, esp. vaccine logistics in the context of the SARS-CoV-2 pandemic, new, energy-efficient vehicle equipment is needed to maintain cold chains. Known refrigeration concepts are designed to cool the entire cargo hold.
In addition, the goods cannot be removed from the vehicle while maintaining the cold chain. An insulating effect of containers is typically achieved by using foamed polystyrene (Styrofoam containers). On one hand, these structures have a very good insulating effect, but on the other hand, they cannot be reduced in volume during recirculation and are problematic with regard to recycling. The aim of the research presented here is therefore to develop a knitted box that is designed as a volume-reducible, rigid but foldable box.
This can be used as a supplement to existing transport container systems and therefore can be inserted in the transport container. The knitted box performs as insulation when the transported goods are actively cooled inside the box. It is a more sustainable and flexible alternative to existing insulation solutions. Knitted fabrics, especially spacer fabrics, have advantageous thermo-physical properties for this application due to their structural design.
In the course of a research project, various spacer fabrics were tested for their thermo-physical suitability as insulation materials. It was found that knitted predetermined folding lines represent an insulation gap. Based on this, a new structure was developed which, due to its structural design, compensates for cold or thermal bridges at vertices and edges of the box. The results show that the knitted corrugated structure insulates better than the knitted spacer fabrics with predetermined folding lines. A thermal imaging camera was also used to identify critical points for heat transfer.
-
Yarn-Level Simulation for Warp-Knitted Clothing Based on Mesh Model
Haisang Liu
1) Jiangnan University, China 2) TU Dresden, Germany
To simulate the warp-knitted product with a specific shape, a mesh-based model for the modelling and simulation is proposed. The three-dimensional geometry of the final fabric is represented as a set of mesh of polygons, each of them containing information about the 3D orientation of the yarns in the warp knitted structure. Using spatial mapping, stitch coordinates from the flat mesh model to the three-dimensional mesh model are transformed and the final rendering is accomplished. The method provides yarn level data for the complete structure and can be used for speeding up the design process of clothing with warp-knitted products.
-
Development of a New Thread Supply for Weft Knitting Machines to Produce Innovative Knitwear
Holderied, Prisca; Mutschler, Thomas; Klausmann, Julia; Heimlich, Frank; Weber, Marcus O.
Hochschule Niederrhein Research Institute Textile and Clothing Technology
Modern consumers of textile products expect fast changing trends, a good availability of products and a larger supply. These expectations make it necessary to shorten the time-to-market significantly. However, the duration of the manufacturing process of a knitted fabric is largely determined by the complexity of the pattern and its related material intensity.
To shorten the production time of known knitting patterns, but also to produce completely new binding types a research team developed an innovative thread supply technology, which was patented in 2018 and funded by the European Regional development Fund (ERDF) as a R&D-project (Funding reference: EFRE-0400310). The presentation introduces the validation process of the patented technology and therefore brings the theoretical considerations into a practical application. The thread supply technology enables the production of a so-called “Doubleface” fabric on flat as well as circular knitting machines. This double-faced fabric consists of two single-faced fabric sides which are knitted by a first yarn in the front needle bed and a second yarn in the rear needle bed. These two fabrics are joined by a third yarn knitting in both needle beds in the same carriage stroke.
This process can generate completely new structures. The method ensures that up to three yarns knit in one system pass. Furthermore, a fourth yarn can be implemented to insert an inlay yarn. The new patterning possibilities arising from the new technology will be presented on the congress.
In addition, the two single-faced fabrics can be produced simultaneously in the same carriage stroke in the front and rear needle bed, separated from each other and followed by a carriage stroke knitting in both needle beds. In this case fewer carriage strokes are required for knitting standard structures such as Milano Rib. This structure can be produced one third faster than with conventional methods.
-
Mathematical Modeling of Dynamic Yarn Tension of a Circular Knitting Machine with Positive Feeding System
- K. M. Mobarok Hossain, Ahsanullah University of Science and Technology, Bangladesh
- Md Imranul Islam, Fashion Institute of Technology, USA
Yarn tension during knitting has a profound impact on fabric quality. Modern high-speed circular knitting machines are mostly equipped with positive feed system, where a predetermined length of yarn is supplied to knitting zone to obtain uniform course length or stitch length (SL). Since SL is theoretically dependent on the stitch cam setting, the constant yarn delivery rate from the positive feed units results different yarn input tension (YIT)- the tension under which yarn is delivered to the knitting zone.
Moreover, using various types of yarn in the same machine may add a noticeable influence on YIT. A plethora of studies addressed yarn tension of the different regions of yarn path instead of dynamic yarn tension for the whole yarn path (i.e., yarn package to knitting needles). This empirical study aimed to determine dynamic yarn tension for the whole yarn path during knitting machine running state and has developed a mathematical model. The comprehensive mathematical model revealed a sum of around 20 knitting variables and constants, that are contributing to YIT at any point of knitting.
The impact of different variables and their interdependence have been theoretically evaluated. Finally, the developed model is expected to justify the reasons of yarn tension fluctuation in a circular knitting machine and thereby act as a key proactive approach for quality control purposes.
-
The visual and physical properties of Croatian traditional knitwear
In this research, attention was focused on the preference for repetition of ornament and preference of colours as well as physical fabric properties of Croatian traditional knitwear. A total of 165 knitted pieces of clothing were found in the Department for Preservation, Reconstruction and Lending of Traditional Costumes in Zagreb; vests, sweaters, slippers, scarves, knitted coats, socks, and decorative wristbands.
The appropriate non-destructive research methods were used since the traditional textile must not be damaged. White yarn, dark blue, burgundy, red, and turquoise blue were five favourite shades of yarn. Purl structure was mostly used for sock and armbands knitting, plain structure for knitted coats, rib structure for socks and vests, and sometimes warp knitted fabric for scarves. The average fineness of the yarn for making scarves was 208 tex, and for massive coats as much as 3513 tex. By far the most popular way of repeating an ornament is translation, where the ornament remains unchanged, i.e. p1., another well used is translation and mirror reflection, i.e. p1m1.
The results obtained from the analysis of fabric contribute not only to the understanding of the originality of character of Croatian traditional knitwear but also allow the production of copies or souvenir production
1POTOČIĆ MATKOVIĆ, Vesna Marija 1PAVLOVIĆ, Željka
-
Knitting Towards Sustainability
Alenka Pavko-Čuden
University of Ljubljana, Faculty of Natural Sciences and Engineering, Department of Textiles, Graphic Arts and Design
Sustainability issues have gained importance both in general and specifically in the textile and clothing sector. In the knitting sector, increasingly close contacts between textile and clothing engineers with textile and nontextile professionals, textile and clothing designers, fibre and yarn suppliers, knitting machine manufacturers, and direct users of knitted textiles and clothing, as well as ICT experts, are dictating strategies for innovative clothing and non-clothing production.
These strategies include measures and define steps for the gradual transition to a circular economy. Sustainability is not just a new approach or a trend that is fashionable right now, but a compelling concept for the survival of companies in the future. At recent trade shows, both machine builders and knitted products manufacturers have demonstrated the adaptation of materials, equipment, and production to sustainable concepts, along with smart manufacturing, cloud computing, cyber production control and robotisation of knitting processes. As an example, the CLEANTEX project is presented, which aims to improve the sustainability of the modern textile sector.
It promotes the adoption of circular economy and eco-design concepts to improve the skills of textile engineering students and workers in the sector. During the recent summer school, students participated in a hackathon whose goal was to integrate circular economy and eco-design strategies into the new production process of a virtual knitwear company.
References
[1] https://cleantexproject.eu/
[2] PAVKO-ČUDEN, A. Recent developments in knitting technology. In: MAITY, Subhankar (ed.), et al. Advanced knitting technology. Cambridge: Woodhead publishing, 2021.
-
Effects Of Fiber Cross-Section Shape on Thermal Comfort Properties Of Polyester Interlock Fabrics
Arzu MARMARALI
Ege University, Textile Engineering Department, İzmir, Türkiye
In this study, some dimensional and thermal comfort properties, i.e. thermal resistance, water vapor permeability, and air permeability properties of interlock fabrics knitted from different cross-section shaped polyester fibers were investigated. Four different polyester yarns of fiber cross-section shapes (hollow, round, triangular, and W-shape) were used to produce the samples. From the results, it was found that the triangular and W-type fibers had higher fabric density values due to the denser and closer fiber settlement.
The highest bursting strength value belonged to the sample knitted from hollow-round yarn which had also the highest yarn-breaking load value. The samples knitted from both round cross-section polyester yarns had significantly higher air permeability and thermal resistance values than the other samples due to the lower fabric density values of these fabrics. On the other hand, the water vapor permeability values of the fabrics from triangular and W-type fibers were slightly higher than the others because of lower thicknesses.
-
Circular Weft Knitting Editor - New CAD for editing of circular knitting pattern and machine settings
Yordan KYOSEV
TU Dresden, ITM, Chair of Development and Assembly of Textile Products, Dresden, Germany
TexMind UG, Heidenau, Germany
The setting of circular knitting machines requires proper arrangement of the knitting needles and all cams. Both together determine the knitting pattern. For the pattern designer the opposite way of thinking is more efficient – he or she has to select the needles types which are required and can place the structural elements - loops, tuck, transfer, pass on selected needles in each row and the cams for these selections are resulting on the element selection.
These both ways if thinking are integrated into the new CAD software from company TexMind “Circular Weft Knitting Editor”. The user can select one of the ways of thinking and the knitting logic is implemented and the resulting elements are set automatically. In this way any errors in the needle, cam or element selection are eliminated. The final result is a well formatted report, which can be exported as PDF, SVG or WMF vector formats for the production. Representation of the loops in 3D is under development.
-
Loop cluster knitted material for Covid-19
Hitesh Kumar Sharma , Knitting Technologist &CQ
An innovation for Covid -19 knitted material in technical textiles is addressed in this paper. It includes anti-bacterial properties, textiles with drug delivery, Perspiration test used while creating loop cluster knitted material.
Day 2 - Abstracts
-
Development Of Innovative Knitted Fabrics from A Novel Combination Of German Hemp And Pure Recycled Wool
Streitenberger, Lisa; Holderied, Prisca; Mutschler, Thomas; Klausmann, Julia;
Heimlich, Frank; Weber, Marcus O.
Hochschule Niederrhein Research Institute Textile and Clothing Technology
Currently, only a very small percentage of textiles are recycled; the majority are incinerated or disposed of in landfills. A major problem is fibre blends with synthetic content. Due to the advancing climate change, responsible use of existing resources is becoming more important than ever before.
The process of rethinking begins in product development with the selection of raw materials.
In the project "CannaReWool" (EFRE-0802000), German hemp and pure recycled wool are spun together and knitted into fabrics. The aim of the project is to produce knitted fabrics that are closed loop recyclable due to their novel combination of materials. Both materials were selected for their low impact on the environment. One focus of the investigation is on different blending ratios in order to be able to measure the influence of the raw materials. In addition, the entire process from spinning preparation to spinning and knitting is evaluated in terms of its impact on the resulting product. The knitted fabrics are produced using the innovative Doubleface technology.
The project is funded by the European Regional Development Fund (ERDF, Funding reference: EFRE-0802000).
All current interim results of the project will be presented in the conference.
-
Development Of A Flexible Flat Knitting Machine With A Device For Continuous Feeding Of Core Components
Mutschler, Thomas
Hochschule Niederrhein Research Institute Textile and Clothing Technology
Tapes and tubes are produced from the technical fibres or yarns as yard goods on flat knitting machines, circular knitting machines, braiding machines and ribbon weaving machines. Knitted products are particularly flexible and drapeable due to the stitch structure.
Profiled hoses with an inserted core are, for example, used as a thermal seal in blast furnaces.
These seals are produced in several operations.
1. Production of the knitted hoses
2. Insertion of the core component
3. Stitching over the entire length to fix the core component and to create the profile adapted to the application.
This method is not only time-consuming but also cost-intensive. So far, there is no possibility to automate this process as a one-step operation, as the production of profile hoses can only be realised on flat knitting machines and there is no continuous feeding device of endless cores for flat knitting machines.
The technical evaluation of state-of the-art flat knitting machines on the market for the processing of technical yarns, the production processes of current technical tubular, and ribbon knitted fabrics, indicates the following problems:
1. Uneconomical production of profiled hoses with inserted core
2. Connected cam boxes
3. Moving holding-down sinkers
4. Low patterning flexibility
5. Increased fibre dust generation
6. Drastically shortened lifetime of needles and needle beds
This paper is highlighting on the technical challenges for the Wing shot insertion in various aspects like:
- Preparation from the endless core inlay
- Connected cam boxes
- Shortened needle lifetime
- Flexibility is lay-out and design from the profile
-
Responsible Performance Knit Within The Outdoor Clothing Space: An investigation into best practice for the design and launch of a responsible range of jersey apparel for the outdoor sector
Fraser Faye, Gault Alison
Ulster University, Belfast School of Art
Charles Ross, a leading figure in the outdoor clothing sector recently stated “In the long term, the environment and the economy are the same. If it is un-environmental, it is un-economic’’ (Ross, 2022). Integration of responsible apparel design and manufacturing processes for any company that occupies space within the textile and fashion industry is now a stark reality, with the proposed launch of an outdoor athleisure brand named Nephin Peaks as part of the cross-collaborative project ‘FUSION ‘(James Arthur Ltd, Intertrade Ireland and Belfast School of Art) the only correct approach could be one centred around such a statement, through the application of a ‘responsible’ design practice.
As part of FUSION, James Arthur Ltd provided an opportunity to do this and with the project lead’s background based in knitted textile design a predominantly jersey knit collection was agreed. This then led to such questions as, ‘Who were the would-be competitors and what was their fabric range’, ‘What was available in terms of responsible innovative knit constructed materials at low MOQ’s?’ ‘What level and type of material performance would be the focus?’
Some of the project leads previous research had been concentrated on developing degradable performance knitted textiles, so knowledge of leading industry yarn suppliers was present but little investigation had been done into what fabric mills were focused on such innovations. As a self-funded start-up label, the balance between the social and environmentally holistic design approach wanted and creating apparel with a reasonable but fair price point to reflect this is challenging, especially with the current economic forecast and the continued tightening of the consumer purse string.
The need for in-depth market material and product research is key for differentiation in terms of product USP (unique selling point), to be a realistic competitor alongside leading industry names such as the US’s Patagonia and the UK’s Finisterre, both with extensive jersey ranges. With continuous new data being released around fibre, additives and manufacturing processes in relation to environmental impact, for example the repositioning of The Higg Index to incorporate post gate use, this project provided the space to review best sourcing and design practice. This required a mixed methodology of quantitative and qualitative research, investigating current market trends within the fibre, material, outdoor and athleisure sectors, interviewing experts within sustainability and reviewing the most up to date research.
The main findings from the research were although ‘responsible’ performance knitted textiles are one of the fastest growing areas within the fabric supply sector the move away from fibre blends using virgin non-renewable synthetics, or new gen synthetics without a closed loop production (effluent processing) is a slow process. Thus the choice mainly fell between provenance or performance, with a lack of fibre certification from many mills highlighting the issue of greenwashing within marketing. Mills such as Pontetorto located in Prato, Italy provided the most comprehensive ranges of innovative knits structures using responsible fibres such as Tencel at low MOQ’s.
-
Slovenian Knitting Tradition
Alenka Pavko-Čuden
University of Ljubljana, Faculty of Natural Sciences and Engineering, Department of Textiles, Graphic Arts and Design
Knitting has a long tradition in Slovenia. It developed from a domestic economic activity through specialized craftsmanship to a well-developed industrial sector. After the First World War, the knitting industry expanded quite rapidly and reached the position of the second most important industry in the country. The towns of Ljubljana, Kranj in the north and Maribor in the north-east became the well-known textile centers. There the industry was supported by renowned educational institutions with a long tradition.
It led to accelerated progress, investments and the development of new products, especially in the clothing and knitting sectors. After stagnation in the 1980s and market contraction as a result of the country's independence in 1991, the crisis hit many companies that were not able to adapt immediately to new circumstances. Privatization and structural change have had an additional impact on the break-up of the local knitting industry. Not all government measures to promote the development and maintenance of employment in this sector have been successful. In contrast to the mergers in the heyday, the large companies were divided into smaller and more flexible units.
Today, the knitting industry in Slovenia is mainly represented by small and a few medium-sized companies producing underwear, sports and leisure wear, technical products and unique knitwear and knitted accessories. The paper presents an overview of the past and contemporary Slovenian knitting tradition, with a focus on design and including both industrial and (handi)craft production.
References
[1] CERAR, E. doctoral disertation. Ljubljana: University of Ljubljana, 2017.
[2] SIMONČIČ, B. et al. TECLO - Textile and Clothing Knowledge Alliance. Future textile and clothing managers for export, marketing, innovation, sustainability and entrepreneurship oriented companies. Project report. Ljubljana: Faculty of Natural Sciences and Engineering, Department of Textiles, 2014.
[3] STANKOVIČ ELESINI, U., CERAR, E., PAVKO-ČUDEN, A. Textile trails in the streets of Ljubljana. Ljubljana: Department of Textiles, Faculty of Natural Sciences & Engineering: Municipality, 2014.
-
Open Educational Resources For Sustainable Knitting Technologies
Prof. Dr.Habil. Mirela Blaga
“Gheorghe Asachi” Technical University of Iasi, Romania
mirela.blaga@academic.tuiasi.ro
Open Educational Resources (OER) are "learning, teaching, and research materials in any format and on any media that are in the public domain or protected by copyright and published under an open licence that permits free access, reuse, repurposing, adaptation, and redistribution by others." Erasmus Plus projects are valuable sources for providing such materials, which can be accessed through e-learning platforms, in the form of educational modules on current textile topics developed for high-quality training of future employees or trainers.
This paper presents the educational modules on sustainable knitting technology implemented within two Erasmus Plus projects, namely OptimTex - Software Tools for Textile Creatives and FashionDIET-Sustainable Fashion Curriculum at Textile Universities in Europe. Development, implementation and evaluation of a teaching module for educators.
-
Irish Spinning: Developing a Local Natural Fibre Supply Chain - Comingling hemp, wool and polymer fibres for sustainable solutions
Steve Howard and Alison Gault
Donegal Yarns Ltd and Ulster University
- steve@donegalyarns.com
- ae.gault@ulster.ac.uk
This paper discusses an 18 month In funded IntertradeIreland Innovation Boost collaboration with Donegal Yarns and Ulster University. The main focus of the research was to identify and investigate potential new products and processes for the company. This included both the development of new yarns from blends and mixtures of natural sustainable materials and also explore the possibility of developing technical textiles for a number of industrial and domestic uses. Irish wool is seen as a category 3 waste alongside animal carcasses, and in recent years has presented a disposal issue, with Brexit and Covid challenges. As a result, the research project aimed to create a yarn from a blend of Irish wool and hemp fibres. The comingling of hemp and wool was specifically selected due to an increasingly growing interest in farming hemp for its versatility in medical, Industrial, and nutritive products but also because of its environmental benefits and carbon sequestration. This paper discusses the results of the blending of natural fibres together including Irish wool and hemp, and also the blending of polymer and Irish wool. The focus on testing waste fibres into viable higher value products for a range of possible end users.
Key words: Fibre, Hemp, Irish Wool, polymer
Speakers
-
Simon Peach
Simon has been working within the Knitwear trade since leaving school, with a focus on Design/Development technician for a wide range of diverse companies, in the UK and internationally. Experienced in garment and product development and production and analogous activities which involved a wide and varied range of yarns, and machinery and programming systems including Shima Seiki Whole Garment, Stoll Compact (Sitix) and also Stoll M1 Plus. Within this time gaining a valued background knowledge and experience of the knitwear industry, enabling him to thrive in his current position as part of the Sales team at Shima Seiki Europe Limited.
-
Thomas Mutschler
Born into a parental home with a knitting factory, his career began after graduating in mechanical engineering from the University of Stuttgart as a service engineer for knitting machines in Japan. This experience was followed by another stay in South Korea for several years as an application and development engineer for textile tools in the fields of knitting, sewing, and nonwoven and carpet production. Extensive experience and expertise in the development of technical and customer-oriented solutions resulted from his work as managing director for production sites for needles and textile machine components in Romania and Portugal.
Before starting his doctorate in April 2018 at the Niederrhein University of Applied Sciences in cooperation with the University of Mulhouse, he had technical responsibility in the field of textile machinery.
-
Eyal Sheffer
Graduated Shenkar College with distinction and achieved his PhD in Textile Engineering in UMIST under the supervision of Prof. Tilac Dias, developing novel 3D warp knitted structures and a way to fabricate them. Returned to Shenkar College in Israel to take a position as a lecturer and researcher of textile technology, CAD and Computer graphics. His research focusses on technical textiles, reinforcement of composite materials, wearable textiles, and parametric design for textiles.
He serves as a reviewer for TRJ and the Accademia Representative in the Israeli Institute of Standards. Currently, Dr. Sheffer is the Chief Researcher of CIRTeX, the Israeli Center of Innovation and Research in Textiles.
-
Yordan Kyosev
Yordan Kyosev holds M.Sc. degree in Technique and Technology of the Textile and Clothing (1996), M.Sc. degree in Applied Mathematics (2002), PhD in Textile machines (2002) (Technical University Sofia, Bulgaria). He habilitated in Textile Technology in Technical University Chemnitz, Germany in 2018. Between 1996 and 2005 he was an assistant professor for Textile Technology at the Technical University Sofia, Bulgaria (design of textile and sewing machines, knitting technology and technical mechanics).
After a research stay with Post-Doctoral Fellowship of the Alexander von Humboldt foundation at the Institut for Textiltechnik of RWTH Aachen University in 2005-2006, he became a Professor of Textile materials, textile technology and quality management (2006) at the Faculty of Textile and Clothing Technology, Niederrhein University of Applied Sciences, Germany. During 2019 he joints Technical University Dresden and take over the chair for assembling technology for textile materials. He developed the 3D module of the first industrial software for 3D visualisation of warp knitted fabrics for ALC Computertechnik (2006-2008).
In 2011 he founded the soft-ware company TexMind, specialized in the development of algorithms for modelling of textile structures, software "Braider", "Braiding Machine Configurator" and "Warp Knitting Pattern Editor 3D", used for creating of the most Figures in the current book. Prof. Kyosev is an author of numerous publications on modelling of textile structures, braiding and knit-ting technology, fuzzy logic. Since 2018 he is an Editor-in-Chief of the Journal of Engineered Fibers and Fabrics.
-
Haisang Liu
Haisang Liu, received the BS degree in Textile in 2018 from Jiangnan University. She is now studying for a Doctor’s Degree (successive postgraduate and doctoral programs of study) program in Jiangnan University. She is also visiting Ph.D student in TU Dresden. Her research focuses on warp-knitting CAD development and warp-knitted fabric simulation, with yarns on complex models represented by tube geometry. Applications are diverse including fabric design software and fabric simulation, which also contains parameter analysis, model establishment, and coordinate mapping.
-
Prisca Holderied
After graduating as a textile design engineer, Prisca Holderied completed her master's degree in technical textiles. During her studies, she did various internships at spinning, weaving, and knitting manufacturers, spent studies abroad at the University Ljubljana and is involved with sustainable textiles in a student initiative.
Since 2019, she works as a scientific research associate in various R&D-projects at the Research Institute for Textiles and Clothing (FTB) at the Niederrhein University of Applied Sciences in Mönchengladbach, Germany. She is doing her doctorate in knitting technology at the Textile Physics and Mechanics Laboratory (LPMT) at the University Haute-Alsace in Mulhouse, France.
-
K. M. Mobarok Hossain
Dr. A.K.M. Mobarok Hossain Is an Associate Professor in the Department of Textile Engineering (Dte) of Ahsanullah University of Science and Technology (Aust), Bangladesh. He holds A Ph.D. In Mechanical Engineering and M.Engg. In Advanced Engineering Management from Bangladesh University of Engineering And Technology, And B.S. In Textile Technology from Bangladesh University of Textiles. Dr. Hossain has a long Industrial background and teaching experience in knitting field. His expertise includes Warp And Weft Knitting, Knitting Mechanics, Quality Control, And Design Development. Dr. Hossain has published 20 research papers In different International Journals.
-
Md Imranul Islam
Md Imranul (Imran) Islam, PhD is an Assistant Professor in Textile Development and Marketing Department at Fashion Institute of Technology, NY. He holds a PhD. in Sustainability in Textiles and Apparel from Kansas State University, MBA in Marketing, MEngg. in Advanced Engineering Management, and B.S. in Textile Technology. Dr. Islam’s expertise includes sustainability, life cycle analysis, textile fibers and yarns, knitting and knit product development, textile testing and analysis, and application of textile technology to design. He is an author/ co-author of over 50 grants, peer-reviewed journal publications, and conference presentations, presented at national and international conferences.
-
Vesna Marija Potočić Matković
Prof. at the Faculty of Textile Technology, University of Zagreb. Scientific research related to the impact of the construction of knitted fabrics on the properties of textiles, and the mutual influence of design and technology.
-
Alenka Pavko-Čuden
Alenka has an HE in textile design, BSc and MSc in textile technology and a DSc in textile science from the University of Ljubljana. After working in the knitting industry for seven years, first as a sewing production manager and then as a research and development manager, she moved to higher education in 1989. She is a full professor at the University of Ljubljana, Faculty of Natural Sciences and Engineering, lecturing on mechanical textile technology, new product development, interior textiles and textile tradition. Her research interests are knitting processes, functionalization of knitted structures and synergy of textile technology and design.
-
Arzu Marmarali
Dr. Arzu Marmaralı is full Professor at Ege University, Textile Engineering Department, with expertise in the area of knitting technology, technical textiles and thermal comfort of textiles since 2002. Dr. Marmaralı authored more than 200 scientific articles published in national and international journals and presented in international conferences. She has published 6 technical books. Prof. Marmaralı is the President of Turkish Section of the International Federation of Knitting Technologists (IFKT) and President of Turkish Section of the Balkan Society of Textile Engineering (BASTE).
-
Julia Klausmann
Coming from a design engineering background, she graduated from Niederrhein University of Applied Sciences as a textile engineer. In the course of her studies, she completed various internships in the production of textile manufacturers as well as at adidas in the product and material development department. Before starting her work as a scientific research associate at the Institute of Textiles and Clothing (FTB) in autumn 2021, she completed a stay abroad at Donghua University in Shanghai and developed eLearning content for vocational school teaching at the Textile Academy in Mönchengladbach. In her current position, she supervises various R&D projects with a focus on knitting technology.
-
Hitesh Sharma
Hitesh Kumar Sharma is a highly skilled knitting technologist, apparel and fashion graduate from north India and CQA from Seneca College, Toronto Canada. He is known as Innovator of Loop Cluster knitted fabric for Covid-19 and worked as Vice President-operations of a knitwear company in Toronto. He joined (IFKT)International Knitting Technologists Association-Germany from Indian national section in 1999. After immigrated to North America he selected as a president to US/Canada national sections in 2018 and later promoted as president of whole North America Continent. He has almost +25 year’s experience on various technical positions in the knitting industry. He always adopting new learning methods and latest knitting technologies on commercial levels in the industry.
-
Richard Pelan
Richard is an Innovation Advisor for InvestNI, Northern Irelands Economic Development Agency. Helping companies to develop their ideas and proposals to seek funding to bring them to commercialisation. Richard started as an apprentice in the aircraft industry before moving into product design. He has won numerous international awards for his work developing products for children with special needs, life-saving equipment for the marine industry and solar collectors and controllers for the renewable sector. Through work with InvestNI and contacts within the Knowledge Transfer Network he continues to encourage collaboration and innovation within our local textile networks.
-
Chris Weiniger
Chris has 28 years’ experience working in the textile industry, 12 years working in the family knitwear business in Ireland and Eastern Europe before joining Donegal Yarns in 2007 as the General Manager.
Sustainability in the textile and clothing industry has gone beyond just using organic materials and efficient processes. As part of his role, he is responsible in leading new product development for existing and new markets.
Having recently successfully completing an Intertrade Ireland Innovation Boost programme in partnership with the University of Ulster, the company has developed some interesting new yarns incorporating locally sourced wool blended with hemp. They worked with an international customer in developing a high-performance yarn blending wool with a recycled extrusion waste otherwise destined for “landfill.”
Based in Kilcar, Co Donegal the company operates a vertical production process from raw wool, through dying, blending, carding, and spinning producing the famous “Donegal Tweed” multi-colour flecked yarn for Machine Knitting, Hand Knitting and Weaving, supplying weaving, and knitting yarns internationally and to leading manufacturers in Ireland/NI. Distribution of sales 60% exported internationally, 40% yarns sold in the domestic market primarily selling under their own brand as well as contract work supplying many of the top international renowned brands.
Chris and the company place a strong emphasis for the future of textiles to focus on establishing and tracking a more sustainable supply chain building strong long-lasting partnerships with both suppliers and customers.
-
Lisa Streitenberger
After vocational training as a clothing technical assistant, Lisa began studying textile technologies at the Niederrhein University of Applied Sciences. During her studies, she became involved in a student initiative on the topic of sustainability in the textile industry. In the course of her studies, she completed an internship in the blowroom and carding development department at Rieter Machine Works Ltd, where she also wrote her bachelor’s thesis on the topic of recycled cotton.
Since May 2022 she has been working as a scientific research associate at the Research Institute for Textiles and Clothing (FTB) in the "CannaReWool" project with a focus on spinning.
-
Faye Fraser
Faye Fraser is a researcher and material specialist, she has previously worked as a knitwear designer in London for luxury and streetwear brands, now with a research focus within responsible material and process development she also lectures within sustainable textile and fashion design.
-
Alenka Pavko-Čuden
Alenka has an HE in textile design, BSc and MSc in textile technology and a DSc in textile science from the University of Ljubljana. After working in the knitting industry for seven years, first as a sewing production manager and then as a research and development manager, she moved to higher education in 1989. She is a full professor at the University of Ljubljana, Faculty of Natural Sciences and Engineering, lecturing on mechanical textile technology, new product development, interior textiles and textile tradition. Her research interests are knitting processes, functionalization of knitted structures and synergy of textile technology and design.
-
Fintan Mulholland
Fintan Mulholland studied at Belfast School of Art, Ulster University and graduated with a first-class honour in 2014 and then completed a master's with distinction in Fashion Knitwear Design at Nottingham Trent University (NTU) in 2015. At NTU Fintan received a Paul Smith Scholarship to study Fashion and Design at Bunka University in Tokyo. His MA knitwear collection received awards including the Institute of Designers in Ireland Emerging Fashion Designer Award.
Fintan designs and produces uniquely constructed luxurious knitwear under his eponymous label at his studio based in Co. Monaghan. He has participated in Brown Thomas Create 2016 and 2018. Fintan also received Best Start-Up Business as Part of Irelands Best Young Entrepreneur 2019 and has recently received the Institute of Designers Ireland Award for Fashion 2021.
Fintan is a part time knitwear technician on the Textile Art, Design and Fashion degree course. He has previously taught part time on the Foundation degree course and BA Textile Art, Design and Fashion degree course at Belfast School of Art, Ulster University.
-
Mirela Blaga
Professor and Ph.D. supervisor at the Faculty of Industrial Design and Business Management of ''Gheorghe Asachi'' Technical University of Iasi, Romania. Her main focus is in the field of knitting technologies, functional textiles and eLearning for textiles. Dr. Blaga recently finished her mandate as president of the Association of Textile Universities (AUTEX). She is the president of the Romanian Section of the International Federation of Knitting Technologists (IFKT) and Chartered Member of the Textile Institute of Manchester (Ctext ATI).
Dr. Blaga is the coordinator of the Erasmus academic exchange program at her faculty. She is an expert and Vice-Chair of the EU Commission for the Horizon Europe research programs. -
Alison Gault
Placement lead for Belfast School of Art, Teaching and Course Director for the BA (Hons) Textile and Fashion Design Course (2007-12) and Course Director for the BA (Hons) of the Textile Art Design and Fashion Course (2013-2018). Placement Lead for BSoA (2015-) Placement Tutor TADF, Consultancy experience with 20+ InvestNI innovation Voucher, 6 IntertradeIreland Fusion/Innovation Boost 18-month Projects, and 3 Propel and HEIF Projects, general consultancy has also included design development of fibres, fabrics and products for health and wellbeing and circular design systems for industry Served as an expert for POST for the UK Gov’t on Education and Industry/manufacturing (2020). Keynote Speaker at InvestNI Textile Forum events on sustainable practice and circular design systems (2016-2020) Subject Lead on the 3 year What works? Student retention and success change programme” Paul Hamlyn Funded project (2013-2015). Visiting Lecturer at Vitebsk Technological University Belarus (2016-2018) and Gheorghe Asachi Technical University (Romania 2015 -17). External Reviewer for Design Institute Dublin (2013). Designer for Pierre Cardin, Yohji Yamamoto, Chanel, La Chasse, Italian Vogue and Barney’s. Consultant Industrial Designer for GlenTara Fabrics, Donegal Yarns, Bonners, JTG, APPAREL MEDICAL, Inis Meain Knitting and Easydry.v
Venue
Ulster University, Belfast Campus, BT15 1ED.
The conference will take place at Ulster University Belfast Campus.
At the heart of Belfast city centre, and will be hosted by Ulster University.
The venue is in close proximity to the historic Crown Bar, the Belfast City Hall and the Europa Hotel.
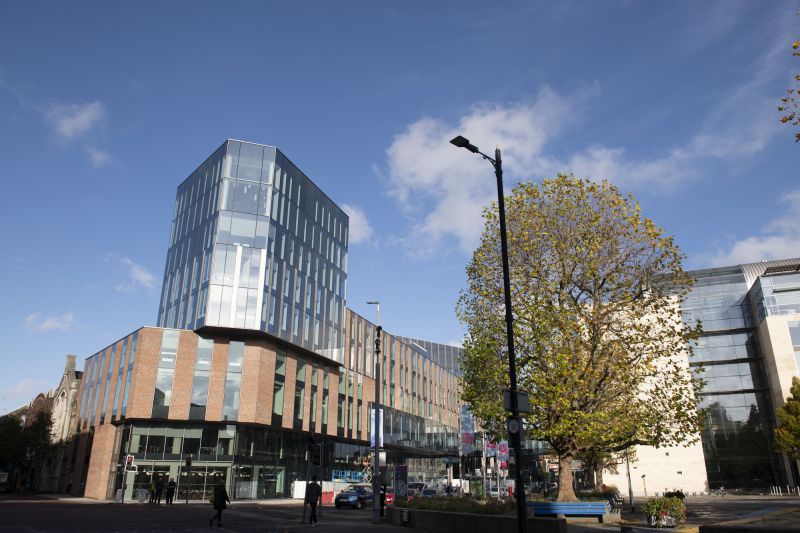
Conference Location
Travel and Accommodation
Flights into:
George Best Belfast City Airport - 4.2 miles/6.75 kilometers
Belfast International Airport – 20 miles/32 kilometers
Dublin Airport – 99 miles/159.5 kilometers
There is a direct bus from Dublin to Belfast every hour.
The following hotels are available to book through our registration portal. Please note that accommodation is not included in the Conference registration fees.
Hilton Belfast City
In the heart of the city centre, beside the ICC Belfast, the Hilton epitomises the lively confidence of the bustling city.
Visit Belfast attractions like the Stormont Parliament Buildings, the Ulster Museum and Belfast Castle. Located beside the ICC Belfast and only minutes from the Odyssey Arena and Victoria Square shopping centre, this Belfast hotel is ideally situated for the conference.
The Hilton Belfast hotel has a business centre and wireless internet access in public areas. From Hilton Rooms up, all Hilton Belfast hotel rooms offer air conditioning and river or mountain views. Executive Room guests enjoy Executive Lounge access and the stunning river-view corner suites overlook the historic Harland & Wolff shipyard, builders of the Titanic.
Ramada by Wyndam
Address: 20 Talbot St, Belfast BT1 2LD
Phone: 028 9026 1800
Relax and explore at our Ramada by Wyndham Belfast hotel in city center near Saint Anne Cathedral. Conveniently located in the heart of town, we offer comfortable, affordable accommodations whether you are with us just one night, or are planning to stay and enjoy the area.
Premier Inn
The Cathedral Quarter was traditionally the home of Belfast's trade associations and warehouses, and still has some of the city's oldest buildings. But a stay at Premier Inn Hotel Belfast Cathedral Quarter puts some distinctly twenty-first century attractions on your doorstep. Come in August and hear some of the latest sounds and bands at the Belsonic Festival. Or December, for a Christmas market that pulls out all the stops. Or in September, for all the fun of over 250 events during Culture Night. Or visit any time of year for world class shopping and fascinating visitor attractions. Then come back to the hotel for mouth-watering food and a lovely comfy bed.
Titanic Hotel Belfast
Situated at the heart of Belfast's Titanic Quarter, the legendary Harland & Wolff Headquarters and Drawing Offices is now the world's most authentic Titanic hotel, offering an unforgettable experience for anyone visiting Northern Ireland on business or for a Belfast city break holiday.
Contact
For more information, contact Alison Gault at ae.gault@ulster.ac.uk.
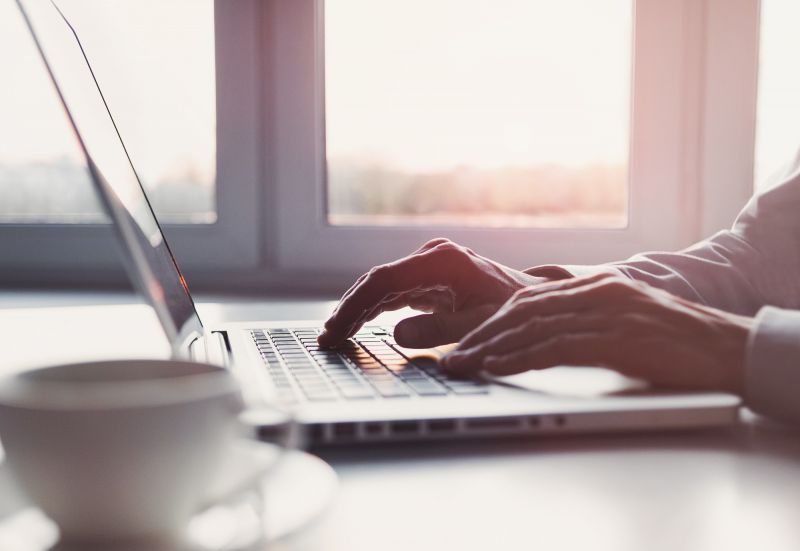